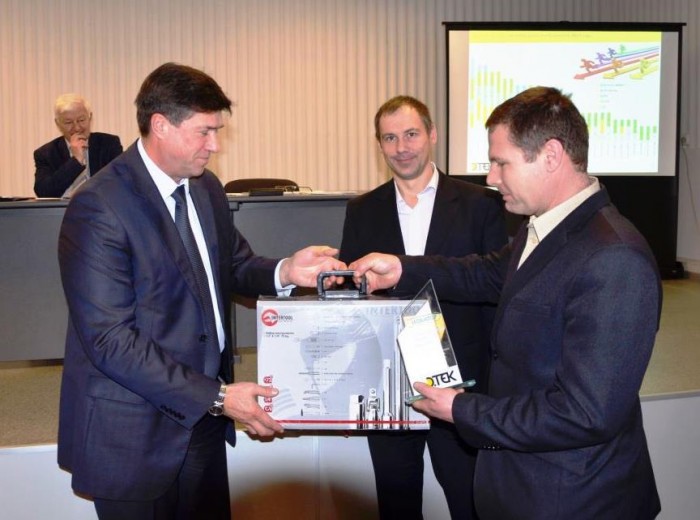
In 2017, the mine management staff submitted more than 1,117 ideas, more than two-thirds of them have already been introduced in the production. Also, specially created teams for continuous improvement (CND) worked on the task of increasing operational efficiency. Special attention of innovators of the enterprise was concentrated on increasing the capacity of skip hoisting. Dobropolskaya due to the reduction of the time of technological downtimes and changes in the operating mode of the lifting equipment.
Participation in the innovative movement for employees is not only an honorable thing, but also useful. So, for submission, introduction and approval of ideas, as well as for participation in teams of continuous improvement, mine management employees received over 827 thousand UAH "premium" during 2017.
The quarterly leader's cup on the effectiveness of the culture of continuous improvement of production was won by the collective of the stationary equipment sector No. 1, (chief Sergei Goncharov), who was recognized as the best among the divisions involved in implementing the Novator SNS in the first quarter of 2017. All conditions for the uniform development of all directions of the Innovator are created on the site: the staff is trained in lean manufacturing tools, the 5C system has been successfully implemented at all sites of the site, CNS is working to solve existing problems, and ideas are being initiated.
Separately noted the effectiveness in the introduction of Innovator workers section number 4 (head Maxim Divulsky) sh. Dobropolskaya, who became leaders in December 2017 to implement the 5C system. The staff of the 4th site is an active participant in the project "Managing Dangerous Actions". In the face, at all workplaces, a store room and a smart section, exemplary cleanliness and order is maintained.
Sergey Derenko, the head of the operational improvement department at the Dobropolskoye SHU, notes:
"The results achieved by the sites of stationary equipment No. 1 and coal mining No. 4, indicate a positive dynamics in the development of a culture of constant improvement in our enterprise. None of our teams succeeded in keeping the leader's Cup in 2017 for the effectiveness of the culture of continuous improvement of production more than once. Four times he passed from hand to hand. This shows healthy competition between sites, the desire of our teams to become leaders of the innovative movement and to succeed in a fair fight. "